An "amateur" suggestion
- Yawen@kth
- Dec 20, 2022
- 3 min read
Updated: Feb 17, 2023
Background
This is a multidisciplinary project. I worked with a mechanical PhD from India, an Industrial Design master student from Sweden and a mechatronic bachelor from Mexico. I basically served as an electronic designer, UX designer and a mechanical assistant in this project.
In this project, we created a mechanical bird that could fly under the moonlight with you. The sensor can detect your raising hands and speed up the wings of the bird, as well as the background moon turning bigger and music louder.
Keywords: multidiscipline, mechatronics, teamwork

Learning via working in pairs
Around 50% of my tasks were on designing and implementing the programs and circuit, 35% on helping and learning about mechanical design, and 15% on designing the storytelling and interaction of the bird. And this distribution of effort, I think, is the most beneficial way for me, as well as for the group. This project is a course project, the aims of which are two: 1) to learn new things; 2) to finish the tasks.
In order to learn, we always distribute the tasks to pairs. A pair will consist of an expert and a beginner. Take the task of implementing the mechanical structure for an example. In the first prototype, I was with Rimmie, the PhD from Mechanical Engineering. With she, I got more familiar with 3D printing, like what kinds of structures are more complex to print and the precision of printing. And in the second prototype, Hala from Industrial Design patiently helped me understand the simulation function in CAD, especially Solid Edge better. By working together, I knew more about different kinds of mechanical connections and the comparison between laser cutting and 3D printing. And for efficiency, most of my tasks were still in coding and designing circuits, as I’m more capable of these with my Electronic Engineering background.

Laser cutting the gears and joints
Challenges in teamwork
The greatest challenge we faced was also cooperation. The four of us are from Europe, South America and Asia respectively, and have different personalities. So there were lots of misunderstandings and intense moments throughout the process. Words like these could be occasionally heard.
“Why did you decide this without letting me know???”
“It’s been two hours now, are you coming or not?”
“I’m done with it! I literally spent so much time on it!”
Yet we never took this personal. Because we all believed that we sounded so hushed, due to the fact that we all cared about this project with 100% engagement.
The most intensive moment we had was around 1 week before the presentation. At that time, countless efforts and time had been spent on the first structure of the bird which inevitably failed to work. Not wanting to admit, we were at the point of a final decision: give up this bird idea or try one more time.
Prototype I didn't work. 3D printed connections were fragile.
I would like to come out better mechanical solution, but I’m not as professional as the rest. Nevertheless, what I did know was that a wise decision was never made in such an anxious and desperate atmosphere.
So I tried to cheer the group up by offering some amateur and ridiculous solutions, such as using rubber bands, buying hinges from Clas Ohlson and glueing the wings. In spite of not being a student in mechanics, I did have some experience in physical prototyping.
Materials I suggested
With the atmosphere released and hope aroused, I further suggested setting a deadline for the last attempt. “If not succeeded before the deadline, we just totally give this up and switch to the backup plan.” And people agreed. Finally, thanks to the solid knowledge of Hala, the functioning prototype II was accomplished. Surprisingly, she did use the hinges and glue!
Iteration of Prototype I
Iteration of Prototype II
It’s a pity that the visual and audio effects I developed were not presented, as I was not physically there and the test was not going well with the rest of the team. The next time when handling something related to hardware, it is never too much to either physically be there, or check the whole system multiple times.
But this is how every journey ends: a happy ending with a little pity :)
Personal contributions
Electronic design
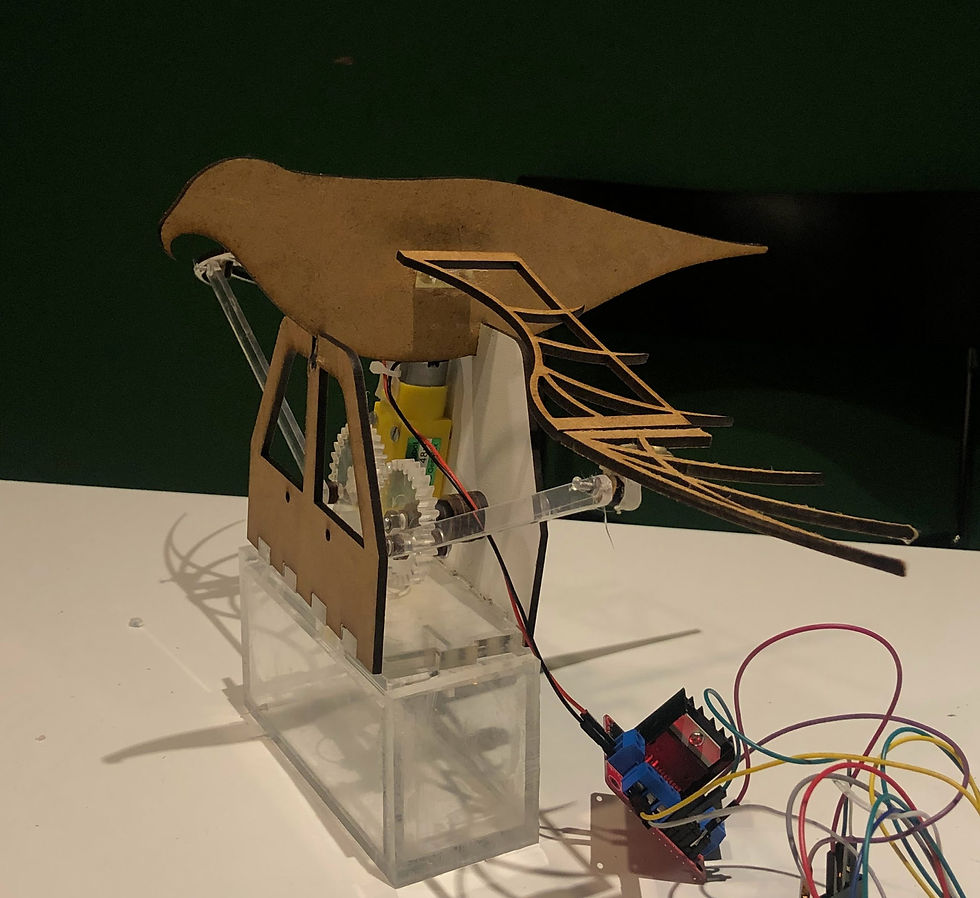
Test and integration
Blooper: Prototype II suicided
Comments